Digitization in the meat processing industry is happening. Recent new builds have shown the dimension of the change, and how much meat facilities are improved through digitization. If it has been a new greenfield project or an upgrade to an existing factory, there are a few things you should observe to get maximum benefits out of your new build and to plan it in a future-proof manner.
One important factor is the sales market. All customers, whether they be wholesalers, retailers, or end consumers are all very demanding. They call for permanent supply capability while keeping response times as short as possible. Downtimes in production or planning faults are difficult to compensate in the day-to-day business.
Another factor is the traceability of products and processes, the importance of which today can never be overrated: after all, trade, consumers and processors themselves want to see the data. The good news is that key technologies on the way to digitization by now have been tried and tested and that they are by far not as expensive as they used to be.
The third and crucial factor is production as such. While complexity and cost pressure is increasing, production should become more flexible and efficient. More modern technologies such as the Industrial Internet of Things (IIoT) and Industry 4.0 bring large benefits for the meat industry.
The following is some experience which Frontmatec has gained and which we can share on how meat processors can step into new projects even better while assuring future sustainability. Of course, these tips can be followed not only in the ideal case of greenfield projects but also for upgrades to existing factories.
Digitization is underway
When slaughterhouses and cutting/deboning facilities manufacture further processed, semi-finished or finished products, from red or white meat, there is always one thing they have in common: Today, management of the value-adding processes is completely unthinkable without digitization.
MES or SCADA are digital tools which are used at all stations – from the entry of the live animals’ these tools with integration to the ERP are the central nervous system of the meat factory, to quality control and delivery of the finished products to the consumers.
Furthermore, digitization in this industry is of significant relevance when it comes to sustainability, product innovations and responsiveness in the modern competitive market. When planning the new construction of a greenfield meat processing facility, one must consider the complex interrelation of technologies, process innovations and consumer wishers.
Consider serious data collection
A consistent data flow is essential as data is the essential raw material of the operational profitability of the factory. Data which is missed or not collected, can neither controlled nor improved. Or it would take many hours of time and effort to do so.
Consequently, one should optimize data management. The required traceability provides the basis that helps to define the data collection points. Barcodes, RFID chips, sensors and image recognition provide a good overview and ensure necessary documentation.
For instance, when data of meat cuts are obtained through instruments during slaughter, this information can be utilized further at cutting/deboning processes and is distributed to crates and boxes labeled with GS1 barcodes, the ERP system may be informed about the key indicators right from work centers on the floor.
To ensure full traceability throughout, the data is tracked electronically from one processing step to the next: From receiving to slaughter, chilling, cutting/deboning and packaging, and to warehouse management including picking and dispatch of final goods.
Never underestimate the human factor
By using new technologies, control systems, machine devices and people work together much more efficiently. As the most “natural” interface in man-machine communication, speech-based technologies help to overcome many obstacles. What works very well in the use of Google, Alexa or Siri can considerably simplify the work processes in the modern production sites.
For example, if an employee is informed to pick for an order of 10 units of trim with 12-15% fat content, the computer voice of the “pick by voice” system could guide the employee directly by most effective route to the correct position of the warehouse. Industry 4.0 professionals combine voice control with other systems such as “pick by light”.
When the picker arrives at the destination, lamps and digits on the shelf indicate the appropriate tray with the available quantity of trim with the requested fat %.
Involve IT professionals early
As already highlighted new meat processing facilities should be looked at as major automation projects. On top of this, information technology is a key element of planning, organization and implementation.
Entrusting a solid industry architectural contractor with planning a new building is normal practice. It may however be common practice for meat processors to have their own internal teams who should have processes in place to make their own decisions, when it comes to the right IT technologies and infrastructures, as these will be highly strategic toward achieving the required return on investment. The choice of an inadequate control system usually will have much more serious consequences than investing in inadequate machinery. A machine could be replaced much more easily and faster than a control system.
The following are tips in finding suitable IT partners:
- Only experienced IT vendors who have solid experience with complete turn-key solutions of greenfield or brownfield projects in the meat industry before will be able to handle the complexity of such projects.
- Your ideal IT partner should have experience in managing complete turn-key projects of various sizes. A recipe for an unsuccessful IT project would be to partner with system provider who is unfamiliar with the meat industry and who has limited experience with integration to your existing or new machinery procurements.
- For new greenfield builds, just like for all projects in the meat industry, it ultimately comes down to real industry knowhow. Only larger concerns who provide mechanical and software with real industry knowledge and background of meat processing will be able to organize your complete digitization process.
Automation and robotics combine data and flow control to perfection
For the shop floor terminal work centers which collect data to material flows, now more and more solutions are available that will increase performance. Added to this, cutting-edge automation solutions have become the backbone of the modern meat processing factory.
The greatest potential currently lies in intralogistics. Many meat companies have developed groundbreaking standards in this area, for automated production and packing facilities, semi-automated picking systems, automatic robot palletizers, sorters and high-bay storage facilities for pallets, stacks or single crates.
Many clients today use a robotic buffer warehouse: Controlled by MES and PLC automation, the single-item containers with attached barcodes are transferred from production to the logistical system and maybe moved to one of several warehouse locations. Small-quantity units are stored in a conventional single-position high-bay storage facility. Fast-moving products, which are sold quickly and in large quantities, go into the fast-mover warehouse.
What is special about this type of storage is that containers are not placed on shelves but stacked directly on hygienic storage floors. One of the reasons for the high performance of the areas may handle several containers, as required, and these may be moved simultaneously during stock entry and removal. In order to assure adherence to the first in, first out principle, the warehouse is constantly reorganized by re-stacking the plastic containers based on the constraints relating to their contents. This process also is controlled by providing a fully automatic controlling system from Frontmatec.
Be in control of improvements by real-time monitoring
One can only sleep easy at night if one can measure and control performance on the shop floor. Therefore, the data-based management dashboarding is the most important element of monitoring in real-time. With the correct, accurate and up-to-date measures, indicators and KPI, one can monitor the performance, to identify deviations from the expected and to intervene systematically to further optimize the factory. In addition to your individual KPI goals, you should therefore have permanent access to the following areas to control your factory in an optimal manner:
Receiving of raw material
Provides the possibility to check the goods directly at goods-in and to document the result in an appropriate control system. This will assist with the assessment of your suppliers and with the proper processing of the goods in your factory. After all, you work with natural products that never have a standardized quality
Production and intralogistics
Mechanical solutions must be reliably with as little downtime as possible. This is imperative for your factories to achieve the operational profitability with production volume goals which one has set. One important measure in this context is OEE (Overall Equipment Effectiveness). In today’s competition, this is one of the most important production indicators as it measures the efficiency of machines, equipment or entire departments, giving an early warning of a process/machine downtime. This results in a better performance of the value-adding departments, shorter downtimes and significantly fewer rejects and missing quantities.
Inventory overview
Keeping track of the stock on hand is a must-have capability for your future factory. This is particularly true for the meat industry where it is the quality and the freshness of the products that count. If you combine intelligent stock on hand monitoring with a reliable forecast of market demands, you can prevent excess stock as well as stock shortfalls and calculate the optimal order quantities. When the minimum stocks are reached in the raw materials or dispatch warehouses, alarm and monitoring tools can be activated automatically. In this way, you can achieve one hundred percent coverage of the material requirements while keeping capital commitment as low as possible.
Gross margin
When all is said and done, one must increase operational profitability with new projects. For this, hard facts are required such as, gross margins, pre-calculation and post-calculation, sales figures per product, customer or country. One can respond better to the developments in the raw material markets, for example in case of increasing slaughter prices for pigs and cattle. Digital solutions can assist here to control the margins with best practices in process.
Ensure systems are future proof
The primary goal of meat processors is to produce meat products and not data, therefore, flexibility and expandability are key. Architects of greenfield or expansions to factories must be very thorough when it comes to the design and its “physical” implementation. Generally, the buildings must be as energy efficient as possible, and the dimensions of the rooms must be variable.
Especially important is a linear material flow direction to ensure efficient production processes. The processing halls layout should, above all, be expandable to a high degree in order to facilitate growth – unless you know today what you will produce in five or ten years from now, and which technologies you will use then. If you build a factory today with a view to a future that is not clearly foreseeable in almost all industries, you should not block your spatial flexibility. This is particularly true for the following areas:
Production and logistics
As a basic principle, the layout should be designed in such a way that the products follow a linear and continuous production path. This can be easily achieved with a square core without columns and as few cornered base areas as possible. Offices could be placed along a side of the hall, while goods receiving, and shipping should be located at opposite ends of the hall. Rooms without columns may be more expensive, yet they provide the required flexibility in case of a short-term, far-reaching change to entirely new product variants, such as cultured meat.
Order picking
The staging zones for transport trolleys and crates are frequently designed too small, which quickly causes space deficits. Therefore, options for expansion should be considered in the high-level concept. Operators routes may be taken into consideration and wave picking versus batch picking maybe considered in relation to what is most efficient for one’s specific order picking goals.
Warehouses and back end logistics
In many concepts, the warehouses are planned and built too small. This mistake can only be corrected through major investments, which means building another warehouse or renting additional storage space. Both solutions are costly in the short and long term. So, one must rather think big when planning warehouse space. A good example here is if one is providing retail packs in pallets to supermarket customers. Delivery faults or indeed fines may be minimized by planning the outbound logistics flow backward to ensure that the correct shipping orders are planned to be ready at shipping bays prior to truck pick-up appointments.
Think out of the box on system integration
For larger organizations, perhaps more than one factory is the plan for optimization. The digitization will maximize its potential if it is integrated across the boundaries of the factory and the corporation. You can flexibly improve your production across all factories and respond quickly to consumer trends, changes in demand for example if the BBQ season suddenly starts due to weather conditions, or particularly favorable prices of certain types of meat in the procurement market.
The top priority for the digitization process should therefore be to update all stakeholders in the value chain to a consistent level of information. Ideally, the aim is to operate always at the limit of the resources, but not of the capacity. The closer you stay with the resource limits, the higher is the average capacity utilization and the use of production means, and the lower is the unit costs. When thinking of this, the following starting points can help:
Minimize inventory
How can one restrict needless physical levels? The more accurately supply chain management requirements can be defined, then the easier such restricting will be. The better the information, the less will you be obstructed by your inventories.
Identify the order penetration point
Up to which stage can the factory produce standard products “anonymously”, i.e. for any customer? At which stage will the customer receive something special? By keeping your production independent of specific customer orders as much as possible, you can manufacture larger quantities and batches under stable conditions. The later you branch into customer-specific production, the better can you plan the entire goods flow.
Analyze and control process chains
Today, the software system allows you to control all relevant stations integrated in the supply chain management process in a transparent manner. For example, animal weights can be planned from the stable up to cutting, distributed to the final products and compared with the expected sales data. Another option is to calculate the planned material costs of the animal in advance up to the final product and then to update the calculation at every station with the actual material costs.
Ensure the ability to adapt to change
The world is moving at a very quick pace. Only a few years ago who would have predicted that us normal humans would be controlling all our personal banking transactions or the heating in our own homes by using a simple application on our smart phone.
Today this is in fact a reality and it would be no surprise if those in meat processing factories were dizzy by the sound of further technologies such as Artificial Intelligence (AI) or Augmented Reality, Cloud, IoT etc. In fact, at the current time AI algorithms and other learning systems still lack efficiency in production environments.
However, this could change abruptly within a few years’ time, as AI not only improves routine processes, but will also extend to creative planning activities. It could however be worth looking even further ahead: Take advantage of brain interfaces as an exciting further development of pick-by-voice or pick by-vision and other brain/machine interphase technologies, production planners should keep focus on the application of “brain interfaces”.
Via electroencephalography and holographic displays, the employees literally control their production machines through mind-reading. Utilize software algorithms apart from that, machines and software will handle many jobs that today are still assigned exclusively to the employees. For example, in quality control, image recognition systems can detect contamination and damage of the meat ever more precisely than and just as reliably as the human operators can. At other stations, the system correctly counts the number of parts and indicates the weight based on volume estimates.
The decisive innovations are not to be expected for the hardware of the cameras and optical measurement and control systems, which are in fact quite advanced now, but in the field of software algorithms, which can perform calculations and comparisons much faster and more reliably than any human being.
Summary
Whether modernization or new building: The key to a successful leap towards the future digital meat factory is an ideal fit of technologies, process innovations and consumer wishes. The subjects as shared here offer orientation and starting points in the context of Industry 4.0 and digitization in order to make well-functioning structures and processes even better.
But that’s not all – every day, exciting, unparalleled, groundbreaking innovations are created by Frontmatec together with our customers. Frontmatec firmly believe that we are a leading automation industry specialist for the meat industry, Frontmatec is an experienced and competent partner to transfer these aspects into the operational practice when building new or upgrading existing meat factories.
As a one-stop provider of MES, SCADA, PLC, hardware, services and business consulting, we optimize business processes and create significant competitive advantages. With our industry specific solutions and best-practice standards including production planning/execution for slaughtering, chilling, cutting/deboning, packing, and full logistics for the meat production, we offer our customers the best solution to any challenge.
Author
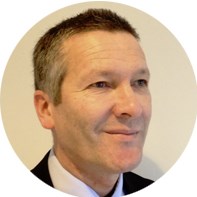
Stuart Mc Bride
Area Sales Manager
smb@frontmatec.com
+4561634547